Discrete manufacturing embarked on the journey to transform traditional factories into factories-of-the-future with the aid of Industry 4.0 solutions years ago. But many companies still have not implemented holistic Industry 4.0 platforms – or else find themselves trapped in “pilot loops,” with little to show for their effort.
Industry 4.0 platforms are often overly broad solutions that require significant upfront investment and are insufficiently linked to solve the most pressing operational problems. Increased business volatility requires manufacturers to be more flexible on production volumes and costs. The benefits of many digital solutions are uncertain, and often do not add value in achieving greater productivity and ensuring a more balanced production, such as a fast product launch, with quick stabilization of output, quality, and cost.
Moreover, there are many unsolved challenges from an IT perspective, including multiple disparate data sources and a weak business logic of interacting key performance indicators (KPIs). Business dashboards, for instance, have been used in manufacturing for many decades, but they focus on simple KPIs reporting such as plant OEE or total production output. Those KPIs, however, are siloed in separate departments and do not provide insights on performance interdependencies; plus, the reporting of operational problems is often delayed.
Exhibit 1: Analytics-based prediction of the production ramp-up curve
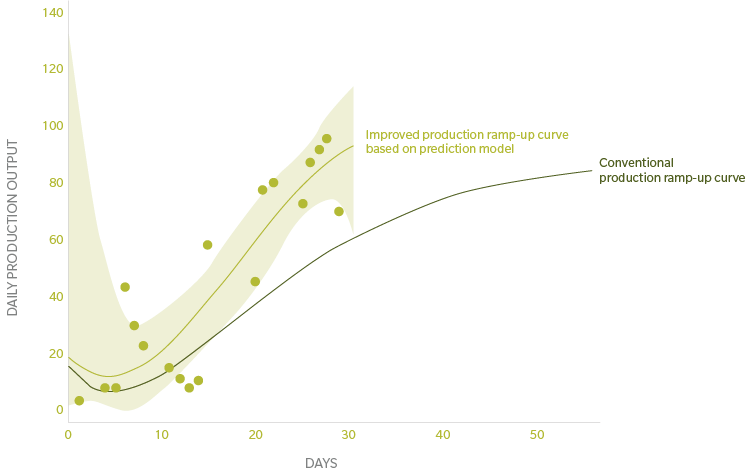
Souce: Oliver Wyman analysis
THE FOUNDATION FOR SMARTER DECISIONS
Building a powerful, agile and value-adding business intelligence platform requires two main components. The first consists in building integrated business logic and KPIs between departments to enable transparent business-performance monitoring. Interdependencies between production, quality, logistics, and human resources need to be defined and linked to the plant’s operational performance. An integrated business logic enables management to understand the cause and effect of underlying production issues and allows them to solve problems quickly. For instance, how do the changes in line speed, operator experience and rework rate impact required buffers sizes and allow a potential reduction in inventory on hand and thereby working capital.
The second component is having the right data sources in an integrated data lake, to fuel the analytics engine for operations performance monitoring. To achieve the selection of the correct data sources, business KPIs and processes must be clearly and precisely defined and translated into the existing data.
NEXT-GENERATION DASHBOARDS TO ANALYZE PERFORMANCE ROOT-CAUSES
The next generation of dashboards must come with the flexibility that lets everyone, from executives down to operators, perform rapid performance monitoring and root cause analysis, such as receiving alerts on negative quality trends or downtime issues. The capability of top plant managers to have a view of shop-floor KPIs, combined with advanced analytics algorithms that identify patterns and root-causes, provides value in decision-making.
For instance, every 250 milliseconds, a battery production plant stores 10,000 variables of data, not all of them related to production. Thanks to integrated production systems, sensors, and logistics, management requires less than 5 percent of those variables to quickly identify any increase in the scrap rate due to the introduction of new materials designed to improve safety, energy density, and lifetime of the cells.
142% faster production ramp-up based on AI predictions
FASTER, MORE STABLE PRODUCTION PERFORMANCE WITH AI-BASED PREDICTIONS
High-stress situations in manufacturing often arise during a new product ramp-up, given the uncertainty of logistics delays, material shortages, line imbalances, spikes in defects, increased rework, and so on. Those factors can lead to a poor ramp-up and a struggle to stabilize production.
Based on historic data of the production systems, advanced analytics models are capable of predicting the production performance learning curve during a ramp-up, which then can be simulated and used for more precise production planning. Two factors are critical to the prediction accuracy: First, there needs to be an array of specific data attributes with sufficient causal connection, such as cycle times, machine availability, defect rates, and operator experience. Second, companies need to select the right predictive model, depending on data structure, prediction complexity, and target.
Being able to predict the production performance based on historical new-product launches is of great value to manufacturers. For example, an automotive Tier-1 supplier used machine learning to optimize output during a new product launch. Using optimized line manning, more precise work-cell balancing, and a production planning per product variant related to historic line performance and product variant complexity, the machine-learning prediction model increased output during the ramp-up by 142 percent, compared to conventional production planning. (See Exhibit 1.)
Digital manufacturing and Industry 4.0 are becoming game changers, both in their business impact and as competitive differentiators. Identifying the levers for improving production, which once required great effort, is something that now can be done in real time. AI and advanced analytics are predicting future performance level and bottlenecks, as well as simulating the results of potential changes in the production plan, allowing management to make correct decisions faster. AI capabilities are certain to grow even more in the coming years, but we have reached the stage where the impact of AI on a company’s performance has become measurable.