Now, however, the trend is becoming accelerated as firms move toward offshoring engineering activities as well. Indeed, the impact on competitiveness is likely to be significant: Industrywide, engineering labor costs account for 30 to 50 percent of total costs and are 75 percent to 90 percent lower in countries such as India, China, or Eastern Europe. Two other benefits have gained importance in line with companies current challenges: It provides an opportunity to penetrate the biggest and fastest-growing markets such as Southeast Asia or Latin America, and it allows companies access to a large pool of highly skilled resources that are growing scarcer in Western countries.
TAKING ADVANTAGE OF MARKET PROXIMITY
The intensification of geopolitical tensions is leading countries such as China, India, and the Middle Eastern nations to boost their defense industry investments, with expected growth rates between 5 percent and 8 percent per year over the next five years. To penetrate these new markets, international defense companies need to have a local presence.
The most pressing incentive to moving work offshore is associated with contractual offsets. The value of these offsets has doubled in 10 years, outpacing market growth and highlighting their importance in negotiations. Some countries, such as India, require offsets of 30 percent, but others can be more demanding, such as the United Arab Emirates (UAE) that require 60 percent. In these cases, companies are pushed to offshore higher value activities, such as engineering. Another important offshoring factor is tied to geopolitical and commercial spheres of influence that gravitate around the United States, Europe, Russia, and China. Export control laws can limit trading options when a product is sold to two different spheres of influence and orientate development and supply-chain options.
Exhibit 1: India and China are training massive number of engineers, while Poland and Romania have already quite a large pool of engineering skills.
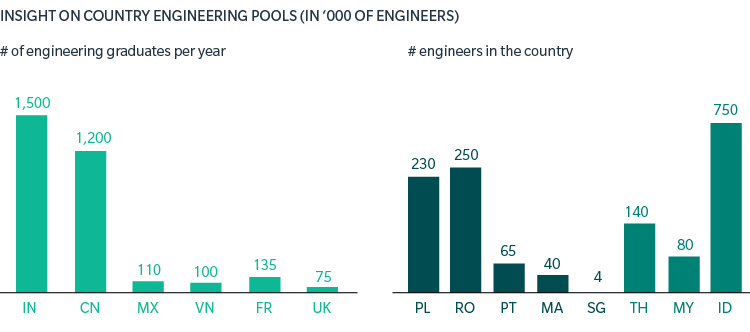
Note: Software Engineering = Data scientist, software developer and web developer | PT: Portugal, PL: Poland, RO: Romania, IN: India, MA: Morocco, AE; United Arab Emirates, SG: Singapore, TH: Thailand, MY: Malaysia, PH: Philippines, ID: Indonesia, FR France, VN: Vietnam
Source: Press review, Oliver Wyman analysis
ACCESSING LARGE POOLS OF EXPERTISE
The complexity of defense equipment, the ever-increasing software integration of their parts and components, and the digital services associated with such innovations have led to new demands and requirements in engineering skills, such as data analytics, cybersecurity, systems architects, and more. Over the past years, this need has resulted in a competitive environment for attracting talent in Western nations, contributing to a talent shortage. Offshoring offers a sustainable solution to this problem, as emerging countries have millions of engineers, each regional pool having its own specialty. (See Exhibit 1.) An engineering center begun in India in 2017 by a leading aircraft manufacturer succeeded in finding needed talent with cutting-edge skills; the center now constitutes more than 1,000 highly specialized Indian engineers.
Talent retention is challenging in these emerging nations, given their high turnover rates. To build a solid relationship early on and to make sure graduates meet the requisite level of expertise, leaders in the defense industry have initiated partnerships with universities in the UAE and in India. Governments are also involved in these efforts, as demonstrated in initiatives by Thailand and the Philippines. While Thailand has made significant investments in digital learning and engineering capabilities, the Philippines has developed a “Cyber Corridor” to create interconnected centers of technology services.
INCREASED COMPETITION
Beyond lower labor costs, emerging countries have launched tax-reduction programs to tip the balance of development costs even more in their favor and attract foreign investment in research and development (R&D). For instance, India offers a 150 percent tax deduction for in-house R&D expenditures while China offers a 50 percent allowance on machinery, equipment, land, and buildings through its R&D tax incentive program.
<15% of engineering workforce offshored, for most Western defense players in 2018
SUCCESS FACTORS OF ENGINEERING OFFSHORING
The defense sector is a unique industry, standing at the intersection of cutting-edge technologies, innovation, national ambition, military strategy and secrets, and the highest technical standards and oversight. The combination of factors adds to the costs and demands placed on the engineering function at companies. To overcome these challenges and stay in the race, Oliver Wyman has identified eight key actions to accelerate and succeed in engineering offshoring:
First, define and establish clear guidelines to ensure collaborators adhere fully to the transfer of activities. Stressing positive motivations – such as additional growth through market proximity, competitiveness, and access to new expertise – is likely to get a better and more constructive reception than an emphasis on competitiveness.
Second, screen your R&D activities to identify which ones to transfer. Build a long-term roadmap: Initially, focus on discrete, non-core engineering activities, such as unit testing or software code development, to build trust. Gradually, however, bigger chunks of development work should be moved offshore, to promote competitiveness and motivate local teams.
Third, create specifications for transferring work early in the process, and make offshore-supplier-management training a must.
Fourth, design a robust local organization and operating model to guarantee quality control of local development. Early on, recruit a local technical leader and a human resource manager.
Fifth, set up strategic partnerships in the target country with engineering services providers to rapidly access trained resources for a quick ramp-up.
Sixth, define the IT architecture that will support the development between the different countries, either through a shared workplace and engineering environment or through data transfers. Cybersecurity and export-control restrictions need to be embedded in the IT architecture.
Seventh, manage cultural differences and domain onboarding by organizing training sessions in Western countries for key local people. Prepare future local managers by pairing them with expatriate managers.
Finally, address the issue of export control licenses early on by involving the Ministry of Defense and sharing the activity transfer roadmap.
Offshoring engineering activities is an opportunity for defense players to benefit from flourishing export markets and take the lead in the talent war. It is also an opportunity for a step change in the engineering processes. The eight key success factors aim at ensuring the sustainability of an outsourcing project and achieving impact in defense projects.