Even in the world that existed long before COVID-19, supply chain management revolved around tradeoffs between the competing goals of cost, service level and cash. Now, however, a dizzying array of factors — including rapid-changing customer demands, unpredictable trade barriers, political instability, natural disasters, as well as the pandemic — has made optimization of the supply chain more challenging than ever before. Achieving a supple and secure supply chain for manufacturers in this new normal will require resilience and flexibility, but cost pressure will remain. The most broadly applicable lever to achieve this is risk diversification which can take two main forms: supplier diversification and supply chain regionalization.
To solve the global supply chain dilemma, companies need to approach future supply chain (and manufacturing) strategy decisions along two dimensions: market requirements, such as product value, complexity, and lead time, and the differentiator value (of having one’s own production capability). That said, there is no “one size fits all” solution: Supply chain strategies will develop in differentiated ways based on the decisions a company makes along the two dimensions.
Market requirements
The key decision for manufacturers in terms of supply chain setup centers on the issue of local versus global production. Factors driving this decision include security of supply for critical products, trade barriers, political landscape, factor costs and skill requirements. While simple and low-value products, such as consumer electronics, will continue to be mass-produced in global low-cost locations, complex and high-value products with shorter lead times, such as medical equipment, will likely be re-localized to increase resilience and flexibility. Indeed, 10 out of 12 industries, with a combined market capitalization of $22 trillion, have already implemented or announced plans to shift back at least a portion of their production from current low-cost locations, according to a recent Bank of America survey.
Differentiator value (of having production capabilities)
Here, the key decision is whether to make or to buy. The factors driving this decision include manufacturing capability, intellectual property, brand, and scale advantages. For certain products, such as engines and powertrains, where perceived customer value and differentiation are strongly driven by production capability, companies have selectively insourced production to build on this capability and ensure independence. For products where the perceived customer value and differentiation are no longer the result of a company’s production capability but rather its engineering or supply chain management excellence, original equipment manufacturers (OEMs) could move toward an outsourced production model to ensure flexibility. However, in such cases, the company should work with multiple suppliers in each sourcing category to avoid the risks of “single sourcing.”
Based on our research and interviews with industry and supply chain experts, we see four manufacturing OEM supply chain archetypes emerging. (See Exhibit 1.) And, depending on the company’s product portfolio complexity, several archetypes could co-exist within one company.
Exhibit 1: Future supply chain archetypes
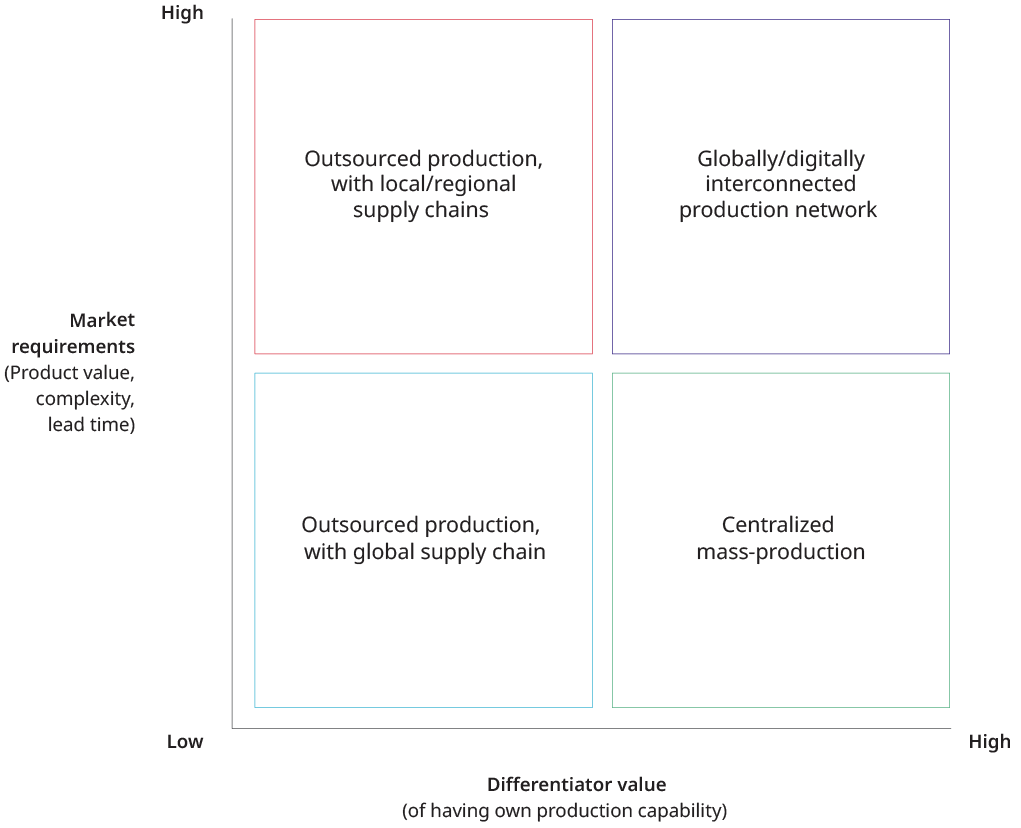
Source: Oliver Wyman analysis
Outsourced production, with global supply chain
Manufacturing companies with commoditized production processes could lean towards a model that outsources production, so as to focus more on value-added activities. If product value and complexity, as well as lead-time requirements, are relatively low, then companies are likely to leverage a global supply chain to optimize cost. This model requires careful consideration of engineering processes, a strong brand, and intellectual property protection to deter suppliers from turning into competitors. For example, consumer electronics is a segment that has begun to adopt this archetype by leveraging Asian-based contract manufacturers that produce their products for the global market.
Outsourced production, with local/regional supply chains
Manufacturing companies with commoditized production processes that need to manage higher-value products and more demanding lead-time requirements, will likely move to regional or even local supply chains to ensure flexibility. Generic pharmaceuticals manufacturers and safety equipment makers are among the sectors that have moved in this direction by managing several supplier networks, each focused on a specific region.
Centralized mass production
Companies with unique production capabilities are bound to keep these in-house to differentiate themselves from the competition. The only way they can offset low product value and complexity is by having global-scale production, maximizing equipment utilization, and implementing cutting-edge automation. By building flexible and highly automated factories, the medical device and high-end electronics industries have started to adopt this archetype.
Globally/digitally interconnected production network
Companies with unique production capabilities that need to manage highly complex products with short lead times are often not able to have their own production facility for each main region, as this would explode their cost base. These companies are likely to adopt a globally and/or digitally interconnected production network to obtain the optimal balance. Automotive OEMs and mechanical-engineering companies are among the industries moving in this direction, orchestrating their supply chain via a global network of suppliers and production sites.
Multiple archetypes may co-exist within the same company depending on the characteristics of their products. As discussed, many factors will influence a company’s decision along the two axes and consequently define the relevant archetypes. As a reaction to the COVID-19 pandemic, we expect to see a shift towards the upper quadrants of the framework, leading to more localized supply chains. Supplier diversification and active supplier risk management are levers that apply equally to the left and right quadrants.
Of course, all these archetypes are related to a specific type of operating model. While there will be differences between the archetypes, all of them share one common denominator: Each supply chain model must ensure rapid responses and flexibility to cope with an increasingly volatile environment, and each must strike a balance between cost, service, and cash. Pro-active supply chain risk management will enable companies to detect potential risks along the supply chain early on to define and initiate the necessary countermeasures.