Facing an industry downturn, the imperative is to slash costs and improve efficiencies at all levels. This necessitates a paradigm shift in their Research and Development (R&D) functions.
Automotive original equipment manufacturers (OEMs) built their R&D functions to serve complex hardware portfolios in times of a rather gradual technological evolution. Among the core competences in this context was the integration of technology and innovations sourced from major (Tier 1) suppliers specializing, on their side, in serving automotive OEM needs. This dovetailed with the OEMs’ own value creation and differentiation through conventional hardware, such as powertrain technologies. The product cycles were long and static, within clearly defined waterfall processes and job splits.
SPIRALLING CONCERNS
These structures and processes have been increasingly stressed by rapid changes in customer expectations and technology requirements in next-generation cars. These vehicles require R&D organizations to deliver functions and systems through integrated software and electronics content, and new “hardware” such as alternative propulsion architectures. Additionally, OEMs have had to reckon with an influx of new tech players pushing into the space. Focusing too much on hardware, they struggled to attract the limited young talent in many core markets offering the skills needed. The existing structures could not always ensure technical product compliance, especially in complex systems requiring know-how from other industries. As a result, even strategic product launches are now facing considerable delays, overwhelming organizations.
These issues have been exacerbated by the COVID-19 pandemic. OEMs have severely restricted engineering capacity due to plant shutdowns and office closures. Initial obstacles in working remotely, or together with limited collaboration modes across functions and partners, are often resulting in efficiency losses. The low buffers, distributed responsibilities, and ongoing delays hinder adaptation of waterfall processes. Potential delays in missing physical parts and materials and lockdowns in offshoring centers are causing engineering chain disruptions. Overall, we assume that R&D throughput has been reduced initially by as much as 30 percent, with some programs completely stopped, and others boosted with additional resources to stick to timelines as much as possible. While some of these issues may be resolved soon, the impact is likely to be more mid-term, with demand uncertainties hindering project prioritization and causing product launch delays. The steep market decline is likely to push companies to contemplate drastic cost measures, trimming R&D budgets considerably while at the same time frantically trying to keep pace.
In the short term, the expected drop in engineering and research & development activity could be 30 percent
How should OEMs close innovation go-to-market gaps and effectively enable budget reductions at the same time? As Exhibit below shows, we believe that they will need to deploy a mix of short- and long-term levers. These include reducing variants, collaborating, reinventing product development processes, and rejigging R&D.
Road towards -30% R&D cost
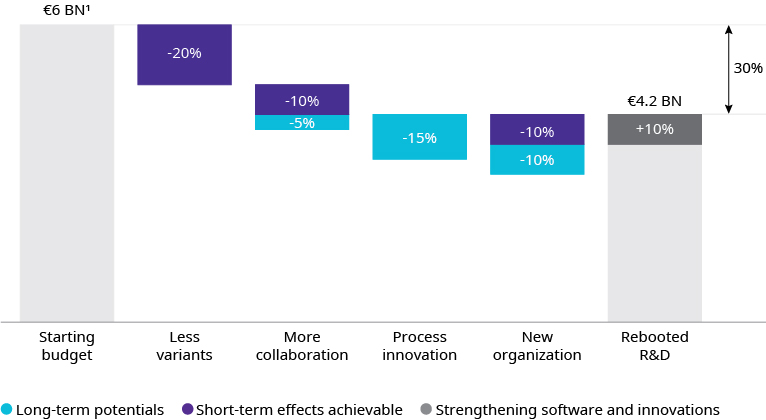
1. Based on average R&D expenditure of major automotive OEMs in 2017-19.
Source: Company annual reports, Oliver Wyman
LESS VARIANTS
The past few years have seen an explosive increase in variants and derivatives as OEMs have tried to capture market niches and profit per vehicle. This has led to a bloated and complex product portfolio, with associated engineering demands for future facelifts and successor models. Trimming the product portfolio is critical in reducing variants and managing development complexity.
More than ever, OEMs now need to review their existing program portfolios critically. With a sharp focus on forecasted demand and strategic importance, they must reprioritize these projects. Now is the time to also question traditional automotive industry rules, such as the seven-years lifecycle: Are there hardware/platform or powertrain elements that can be upgraded to serve longer times?
From derivatives planning down to powertrains, options, and features, we expect that the more aggressive OEMs will cut down variant development programs by as much as 30-50 percent. Only a radical move will enable R&D functions to shift critical capacity to the disruptive technologies they will need in coming years.
MORE COLLABORATION
OEMs will continue to rely on supplier product innovation to create a large part of the value, but now they may need to refocus these partnerships towards saving cost. This could entail collaborating with key suppliers to jointly identify process innovation and cost reduction potential, master a set of capabilities which are hard to master alone, or even develop bundles to meet changing customer needs. We find that such collaborations could lead to approximately 30 percent more ideas and create an approximately 20 percent higher margin potential. However, this also requires OEMs to proactively manage potential pitfalls like legal issues, limited willingness to make changes, misalignments, poor execution, inadequate processes/tools, and “old school” purchasing habits.
At the same time, many OEMs will increase collaboration with other OEMs, even in strategic areas such as electric vehicles and software. This could be in the form of tech alliances and sharing platforms for emerging technologies. On the other end of the spectrum, OEMs will need to bundle efforts in mature or declining technologies.
PROCESS INNOVATION
In addition to looking into portfolio and collaboration, OEMs must also adapt their processes. The starting point at any OEM R&D function is typically a detailed waterfall-driven product development process (with industrialization elements at OEM and suppliers in parallel), defining the daily work of a large proportion of the developers and engineering towards key milestones.
Though hardware and software development cycles are vastly different, OEMs need to deliver on both in new vehicles. System engineering principles offer one potential solution to blend hardware and software development and deployment capabilities. The following article written by Oliver Wyman Engineers dives deeper into how OEMs can adapt their product development processes to achieve this.
At the same time, other parts of the organization work in largely unstructured ways as there is no clear “technology development process” defined yet. Here, a completely new working model, based on benchmarks from the tech sector, may have to be developed as OEMs increasingly refocus and mature their inhouse innovation capabilities towards software and architecture.
THE NEW R&D ORGANIZATION
Finally, OEMs must rejig their R&D to capitalize on changes to activities and processes in the long term. In the short term, this requires OEMs to reinforce workforce planning and program prioritization to enable frequent and dynamic resource reallocation. Further, researchers and engineers are typically efficient and intrinsically passionate in program crises. In that sense, the existing concerns surrounding R&D functions offer an opportunity to mobilize research and engineering capabilities to overcome the current overstretch.
These changes to R&D merit additional modifications to how the function is managed and run. In a sense, OEMs need to run R&D like a factory in the future. This requires undertaking a systematic benchmarking of the organization and orienting towards key performance indicators (KPIs). It is important to note here that the traditional KPIs used in the past for R&D functions are limited in what they measure and benchmark, given the changing nature of the activities, processes, and organization. Thus, there is a need for alternate KPIs aligned with the new realities under which revamped R&D organizations must operate.
By pulling these four levers aggressively, OEM R&D functions will be able to cut down cost dramatically, even beyond the overall efficiency targets imposed on them. This will create headroom to build-up new in-house competences, which will be an essential pre-requisite to close the gaps to tech players pushing into vehicles and mobility ecosystems.
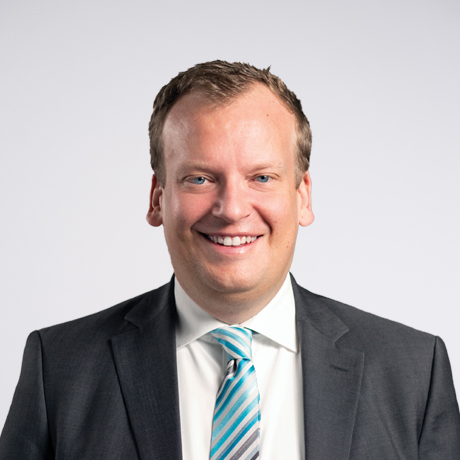
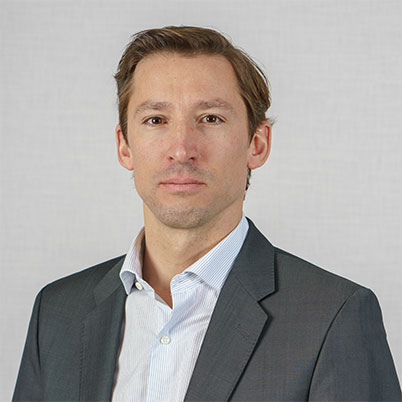
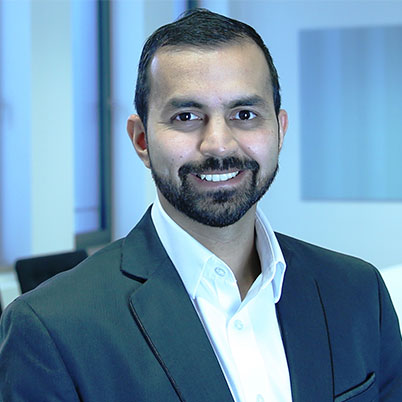