With the rise of strong competitors from the Far East over the past 30 years, the industry has become more fragmented and challenging. This has benefited the customer, because tougher competition has resulted in the debut of more new models that possess better features, provide better performance, and offer better safety than ever before. Automakers have been forced to make huge manufacturing improvements and as a result plants around the world have achieved levels of quality and productivity that few thought were possible. The gap separating many companies is as close as ever. In fact, when J.D. Power first measured the quality of new cars in the United States, the ratio difference between the best and the worst brands was almost 10-to-1. Now, it is less than 2-to-1.
Alarmingly Wide Gaps
Developing a new vehicle from an idea or concept, then conducting the engineering, tooling, launch, and eventual mass production takes four to five years and costs billions. Every car company knows this is a cost of doing business, but it is wrong to assume that those capital costs are the same for all competitors across the industry. Recent research shows there are alarmingly wide gaps when comparing the money invested by the various manufacturers to bring a new car to market.
Today’s automobile companies have narrowed their businesses in recent decades to focus on three major areas of in-house production:
- Metal forming/stamping
- Powertrain (engines and transmissions)
- Vehicle assembly
A closer look inside the car assembly plant shows where the investment gaps exist. Vehicle assembly plants today have four main processes:
- Metal stamping (which is sometimes outsourced)
- Body welding
- Body painting
- Final assembly
It can cost more than US$1 billion of capital to construct a factory to produce 1,000 cars per day. Whether building an all-new model or adding another vehicle to an existing plant, money is required for new dies to make doors, hoods, fenders, and all the other body panels. New tooling is needed to hold body parts while they are welded, riveted, glued, or lasered. Money must be spent to replace or reprogram robots. New molds are necessary for bumpers, instrument panels, and trim parts.
An examination of different vehicle programs and plants among various competitors shows that not only are these costs different, the gaps can be significant. Examining the chart on the next page, the cost for a common set of dies to produce a given set of steel body panels can vary by a ratio of 3-to-1. The difference in the cost of the welding equipment in the body shop can be even greater. Also, it can cost twice as much to provide product for the same volume in one paint shop versus another. Why do these differences exist? The companies showing benchmark investment performance are also the most flexible and display some of the highest efficiency and quality in the industry. Let’s examine why.
Critical Decisions
The body weld shop is complex. Typically 4,000 to 6,000 welds are made to attach and secure the various metal parts to each other, creating the body that will then be painted and the multitude of parts attached to it. This process must be done right or nothing else will fit or look right. Every company engineers the steps and tooling to perform this task. A number of critical decisions will affect success here.
Commonality: Some automakers excel at developing vehicles that look different but underneath they share multiple key parts and, most importantly, processing. This allows multiple vehicles to be built on one production line.
Flexibility: Some companies have developed systems that can weld numerous different models in the same system, eliminating multiple tooling. This requires less floor space, less energy, uses fewer people, and saves money.
Reusability: By maintaining a relatively common process or sequence build from the old model to the new one, a company can reuse elements of the same system and only has to replace the specific tooling that holds the product in place. This can save 70 to 80 percent of the investment cost when switching from the old model to the new one.
In-house engineering: A common denominator among leaders is that the design, engineering, and construction of key elements of the tooling and processes are done internally. These manufacturers believe that developing a production process that is unique, flexible, and lower cost is a competitive advantage.
Conflict of interest: Little motivation exists for tooling suppliers to work toward competitive levels of capital investment for their customers. Certainly, they have to be price competitive, but higher prices mean more revenue, while less flexibility means regular replacement of the process rather than reusability.
Simplicity: Ironically, the most competitive plants, whether measured based on capital efficiency, quality, cost, or productivity, are not the most automated. Those that successfully balance today’s high-tech machines with the right amount of human support do the best. Too much automation can add superfluous cost and complexity.
While many areas of factory efficiency have narrowed significantly in recent years, capital efficiency remains dramatically different. Many companies don’t even know or believe that this gap exists. It is clear that an automaker can’t offset this cost by increasing the sticker price, because no car buyer would be willing to pay US$300 more at the dealership to cover the cost of an inefficient weld shop for example. Those automakers that capitalize on the potential savings in this area of the business use the money to add new features, update materials, or improve the performance of their vehicles. Therefore, is this a capital idea that has gone unnoticed?
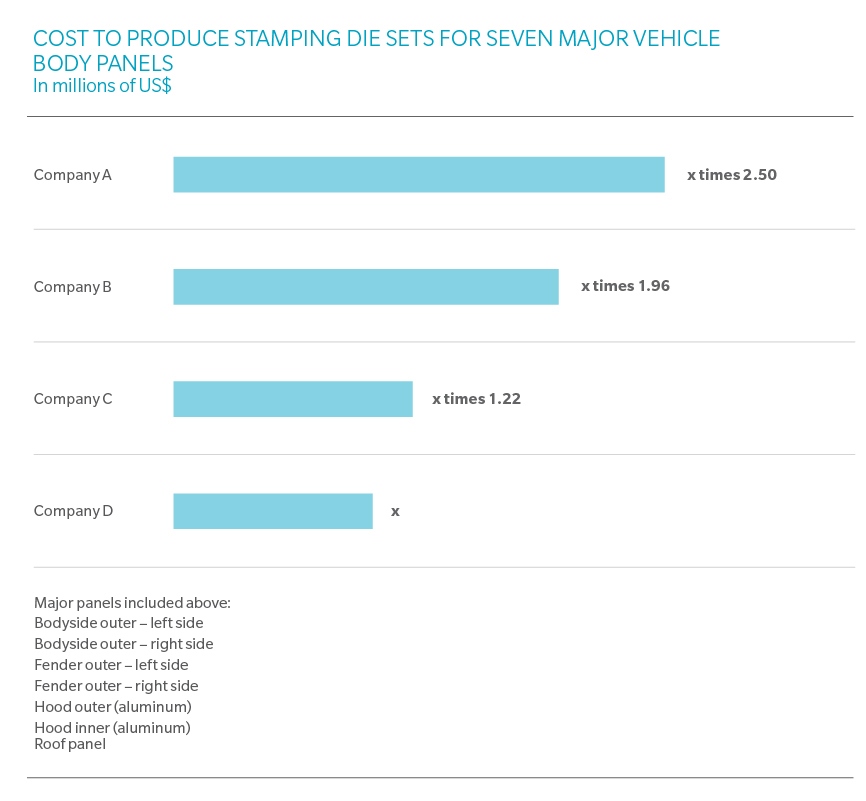