For the past several years, post-global recession, automakers and automotive suppliers have been straining to recruit engineers fast enough, and the problem only appears to be getting worse: In the United States, 69 percent of respondents to a recent survey by the Original Equipment Suppliers Association (OESA) reported that “engineering talent or availability” would be an internal issue in 2015, impacting the need to meet increased levels of production. And when it comes to new product launches, 57 percent cited engineering talent as a most significant or significant risk. Similar situations exist in other automotive centers, such as Munich and Stuttgart in southern Germany, where unemployment rates for specific types of engineers have dropped below one percent.
Why aren’t there enough engineers to go around? In a sense, the automotive industry is facing a perfect storm when it comes to talent: Talent flight during the recession, especially in Detroit, an aging workforce, healthy business growth, and a greater demand for engineers overall (and with more diverse skill sets) at both automakers and suppliers, in response to an increase in high-tech components in cars and a push for innovation. At the same time, disruptive technology companies, such as Tesla, Google, and Apple, are entering the automotive arena, increasing competition for the most skilled members of the talent pool. Finally, generational changes are impacting “where the engineers are,” what they want from their careers, and even if they want to enter the automotive field in the first place.
Changing Demands – And Culture
According to OESA’s survey, suppliers of electrical/electronics, powertrain, and exterior components are all reporting talent shortages, with an increasing cost for talent as a key constraint. Things are even worse for automotive software engineering. Globally, automakers see a need for stronger engineering skill sets in the areas of electrification, hybridization, advanced propulsion, and software. There will be a critical requirement in the next five years to add expertise in the growth markets of Mexico and China.
The entry of disruptive technology companies into the automotive space is particularly putting pressure on the high-tech end of the talent pool – even to the extent of siphoning off engineers from other technology companies to meet their needs. For example, Tesla has been hiring more engineers from Apple than from other carmakers, leading to escalating compensation. Apple has started pulling in engineers from automakers and suppliers for its skunk works to develop an electric car. Similarly, Google is investing heavily to develop autonomous vehicles, reportedly hiring away talent from large automakers which then in turn are taking talent from suppliers. Accusations of poaching – and even lawsuits – reflect the extreme strain companies are now under to get the skills they need to compete effectively.
The promise of making cutting-edge cars and components, while supporting environmental sustainability, make electric and hybrid automakers particularly appealing to young engineers. Location also matters: In the US, few young engineers are interested in moving to Detroit; they want to stay near centers of innovation and tech culture. This has led to traditional automakers setting up and expanding R&D units in Silicon Valley. Ford is the latest to the party, recently opening its 125-person Research and Innovation Center in Palo Alto (led by a former Apple engineer).
Another challenge with regard to talent is that the traditional job security offered by automakers is less appealing: 70 percent of Millennials typically change jobs every two years, according to Kelly Services. And Millennials rate flexibility as a top perk – making contract work more attractive. (By 2016, more than half of US workers are likely to be independent contractors.)
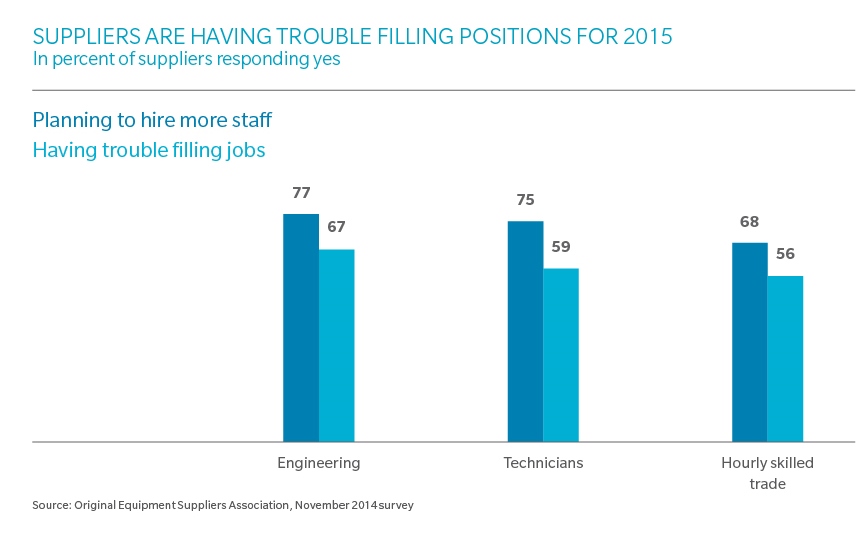
Expanding The Pipeline
As the above trends make clear, suppliers will need to move faster on several different fronts to keep up with an evolving workforce and the automakers’ “talent contest.” Suppliers will have to cast wider cross-industry nets and build automotive training programs to fill in gaps for engineers from other industries. They will need to strategize on how to appeal to millennials, such as through the promise of R&D opportunities and co-location with other tech companies. And with interest waning in job security and a long career at a single company, suppliers may need to develop efficient engineering services outsourcing programs, offering more project work on long-term contracts.
The lack of a sufficiently robust talent pipeline, however, starts with not enough young people considering automotive engineering as a career – or realizing that high-tech skills can be translated to the automotive industry. In response, suppliers (which historically have been more passive in this regard than the automakers) should be reaching out to the next generation by encouraging students in their local communities early on to pursue STEM (science, technology, engineering, and mathematics) careers, and then following through much more broadly and visibly by supporting local university automotive engineering programs, including graduate-level internships and apprenticeships.
This last step has been shown to work: Companies in Germany and Sweden, such as Volvo, BMW, and Audi, report experiencing less recruiting strain precisely because strong ties with universities and graduate-apprenticeship programs have been the norm in these countries for some time. Audi, for example, has partnerships with some 29 universities. In the US and UK, such programs are less developed, but there have been promising developments: Bosch, for example, is funding fellowships for women and minorities at Clemson University’s automotive engineering graduate program; while in the UK, Jaguar Land Rover and Bentley have expanded their apprenticeship programs.
The other end of the pipeline is redesigning strategies to retain workers and increasing succession planning. There may be a need to develop more flexible options for the most skilled resources as well as for older workers thinking about retirement, with the goal of ensuring that training and know-how get passed on.
In summary, the challenge for suppliers of getting and keeping engineers is unlikely to go away anytime soon, and may get worse. Skyrocketing compensation and poaching may scratch the itch but they aren’t good long-term solutions. Innovation, flexibility, and investment will be as important to meeting future talent needs as they are to building the next generation of cars.