This year marks a long-awaited decline in semiconductor demand. But for many industries, the supply problems that began in the pandemic will continue to be business as usual.
A prime example is automotive. While global semiconductor sales are projected to drop to $623 billion in 2023 from $639 billion last year, according to analysis by Oliver Wyman, demand in that sector just keeps rising. With a three to five times increase in chip content per car — driven by electrification, functionality, and increased penetration of Advanced Driver Assistance Systems (ADAS) — sales are expected to jump to $90 billion in 2025 from $61 billion in 2022.
That’s a hard pill to swallow for automotive original equipment manufacturers (OEMs), which suffered a combined production loss of approximately 13 million cars in 2021 and 2022 stemming from semiconductor supply chain issues. The industry is hardly alone: Most of the problems are with trailing-edge microcontrollers, which a wide range of businesses need. Over the last five years chip makers have invested far more heavily in leading-edge semiconductors for which they can charge higher prices, and now will require two or three years to build out trailing-edge capacity. In the meantime, automakers and other companies might lose billions of dollars in profits due to shortages of trailing-edge semiconductors.
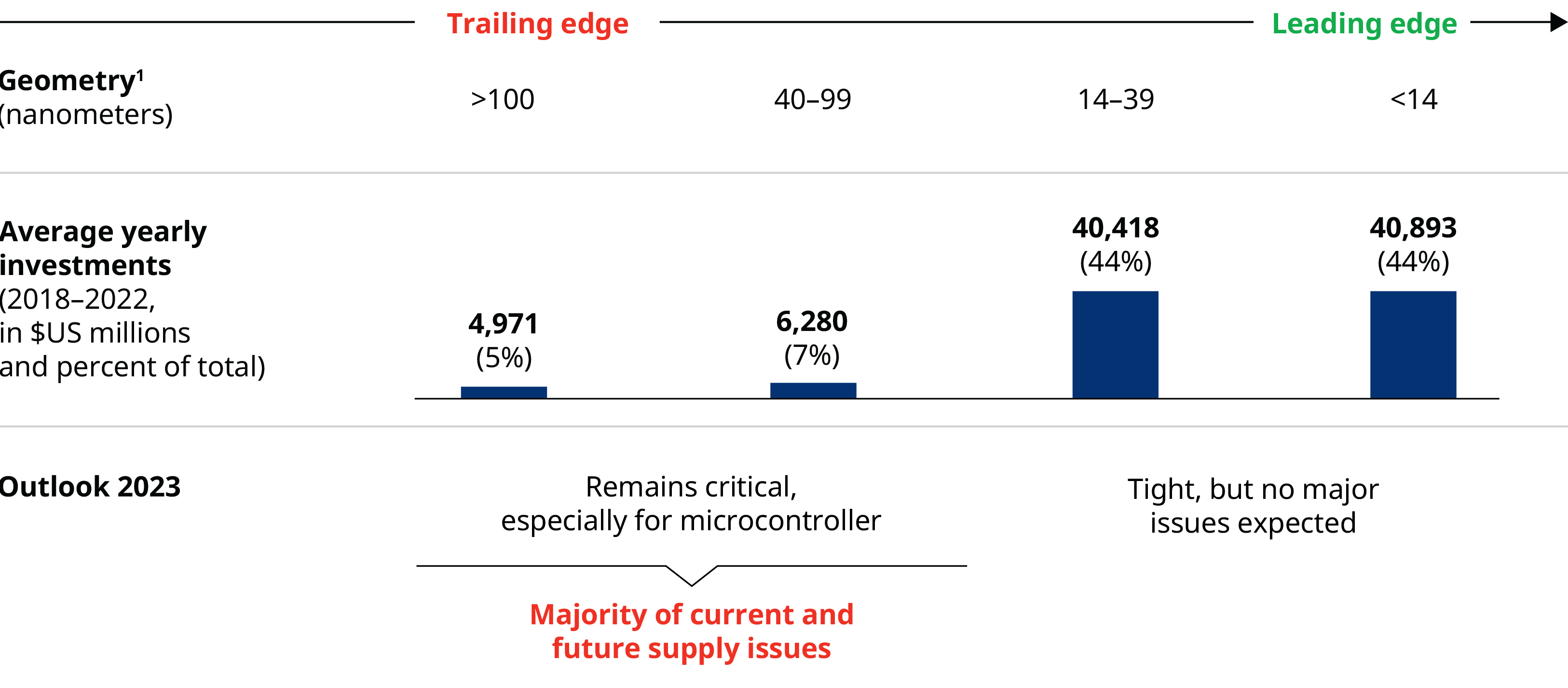
1. To differentiate by memory and logic
Still, the experience has provided valuable lessons for how automotive OEMs and other companies work together with semiconductor makers. Moving forward, they need to turn what they’ve learned into action if they hope to avoid the same kind of shortfalls from occurring in the future.
Managing semiconductor supply chain risks
For OEMs, an effective plan will have short-, medium-, and long-term components. First, to address immediate challenges, businesses should launch an internal task force charged with creating transparency around semiconductor supply chains. It’s a continuous process of identifying potential risks, as well as preparing measures — anything from spot market purchases to using alternative components — to enable fast reaction times. Given that shortages often come up with little advance notice, the task force can benefit from meeting as frequently as every day if necessary. For the most pressing issues, the board may need to become involved as well.
Looking ahead to medium-term solutions, companies like automotive OEMs and tier-1 suppliers must focus on managing the existing supply chain for resilience. That means more formally defining their strategies for avoiding and mitigating risk, including how they prepare for crises. First, the organizations should identify their semiconductor demand based on their production schedule, and then pass that information through the supply chain. Next, they must help put semiconductor manufacturers in a better position to meet that demand by communicating it directly to them.
Measures that set up the supply chain for long-term resilience and minimal risk are important, but also costly. With this balance in mind, organizations should carefully weigh their approach to handling suppliers, partners, governance, and other issues. There is a large breadth of options worth reviewing for the most important semiconductors, such as increasing inventory and stock levels, moving to dual sourcing, and offering incentives to suppliers.
How chip makers can help meet demand
Semiconductor companies also share in the responsibility for preventing shortages. It’s vital that they increase collaboration with automotive OEMs and any other companies in industries that are becoming more important customers. It starts with encouraging improved communication about future demand. Ultimately chip makers need to work hand-in-hand with such clients to align buildout and investment plans, similar to the relationships they’ve long had with tech companies.
Of course, none of these are one-off steps. Translating the learnings from two years of supply chain woes into organizational capabilities takes persistent effort. Over time, smart businesses will strive to make those capabilities permanent.
Felix Diehlmann also contributed to this article.