The global COVID-19 pandemic may have ended, but the supply chain problems that came with it have not. Every day, many supply management teams are contending with resource shortages, supplier lead time changes, and new difficulties like the semiconductor crisis and overseas transport issues. The situation leaves them in constant firefighting mode, while also facing increased raw material stock levels. To reconcile the competing needs for inventory reduction and production stability, manufacturers have launched initiatives to move from a reactive "missing parts chasing" approach to a proactive coverage monitoring strategy.
Making such a transition is easier said than done, however. Whether companies produce high-volume consumer goods or complex, low-volume products like trains and aircraft, they often struggle to embed coverage monitoring within their organization and supply chain teams, so that they can frequently review coverage for individual parts and engage early with suppliers.
The difficulty stems, first, from the lack of a sophisticated tool to calculate optimal coverage for every part number based on factors such as supplier delivery performance, damages during production, and demand volatility. Second, organizations may underestimate the effort they need to reach full adaptation of the new tool and related processes. We often see limited trust in the proposals to implement changes, as calculation rules are poorly communicated, guidelines are inadequately defined, and the impact of false safety parameters remains unknown.
How shifting operational modes can yield big results
For most original equipment manufacturers (OEMs), 40% of missing parts are caused by suppliers which have occasional issues that could be avoided through early anticipation. Our work with clients has demonstrated how properly adopting a new coverage tool — complemented with an adjusted governance model and a shift in management and working level mindset — can address that issue, significantly enhancing supply chain resilience and reducing costs.
In one recent project, for example, a leading manufacturer of protective paints and coatings reduced inventory by 15%+ and improved fill rate to 95% from 85% within six months. The company projects an additional 15% inventory reduction, as well as reaching their fulfilment target of 98.5%, within a year of the start of the engagement.
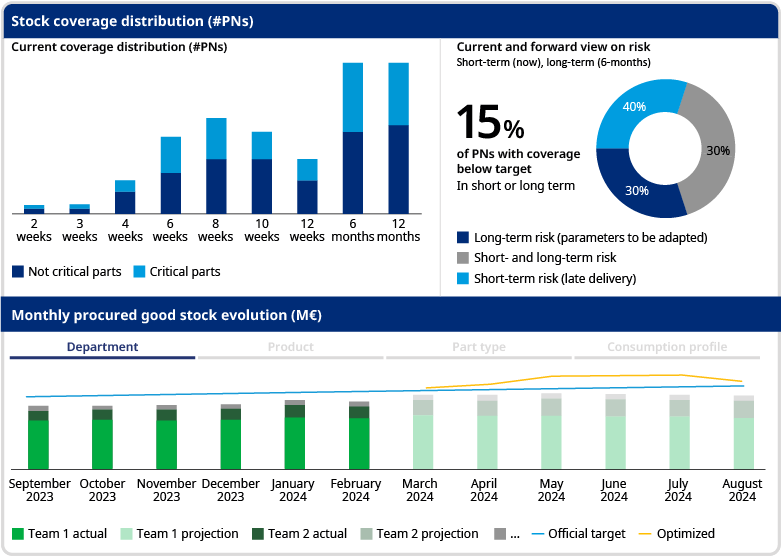
Implementing the optimal tool for supply chain resilience
Again, such a move to a proactive resilient coverage management approach won’t happen overnight, and any organization that hopes to pull it off successfully will need a serious kick-start. The foundation is the deployment of a tool that projects stock needs based on collected data, with a concentration on parts at risk. It must be simple to understand and relatable for the operational teams, for example, they need to have the same figures available in their enterprise resource planning (ERP) system and easily recognize risks identified by the tool like demand volatility and forecast accuracy.
With the tool in place, companies can set targets that prioritize supply chain stability and resilience. They can also provide guidance on the minimum coverage required to withstand supply chain risks, particularly for critical parts (for example, no parts should have less than two weeks of coverage, and no more than 15% of parts should have coverage exceeding six months).
Essential organizational changes manufacturers must make
Broader changes within the organization are also crucial. Management must foster a proactive culture that values risk mitigation over firefighting, for instance, motivating working teams to reach out to suppliers to ensure purchase order delivery dates will be met even for less-critical parts. It also must develop hands-on training initiatives with real, relatable examples to equip employees with the necessary skills and knowledge to effectively understand, manage, and adapt to the resistance approach. With the proper execution, the new strategy will eventually become an integral part of the organizational structure and yield the promised results.